Fra-Ri Press. Experience, reliability and innovation.
FRA-RI
Specialists in forging brass alloys, since 1989.
01
HIGH QUALITY STANDARDS
Modern facilities, cutting-edge machinery and specialized personnel guarantee high quality semi-finished products.
02
FLEXIBILITY IN DELIVERIES
All processing phases are managed internally within the Company, optimizing production costs and times.
03
SAFETY FOR PEOPLE AND ENVIRONMENT
Safety in our departments and environment is guaranteed by strict compliance
with current regulations.
THE COMPANY
By choosing Fra-Ri Press, you choose experience, reliability and innovation.
Founded in Valduggia, a Valsesian hub specialized in the production of taps and valves, the Company has acquired an important commercial legacy and has since established itself as a point of reference in the sector.
Fra-Ri Press focuses on the forging of brass alloys, a process that allows us to offer uncompromising quality, flexibility in deliveries and a constant commitment to safety in the workplace and for the environment.
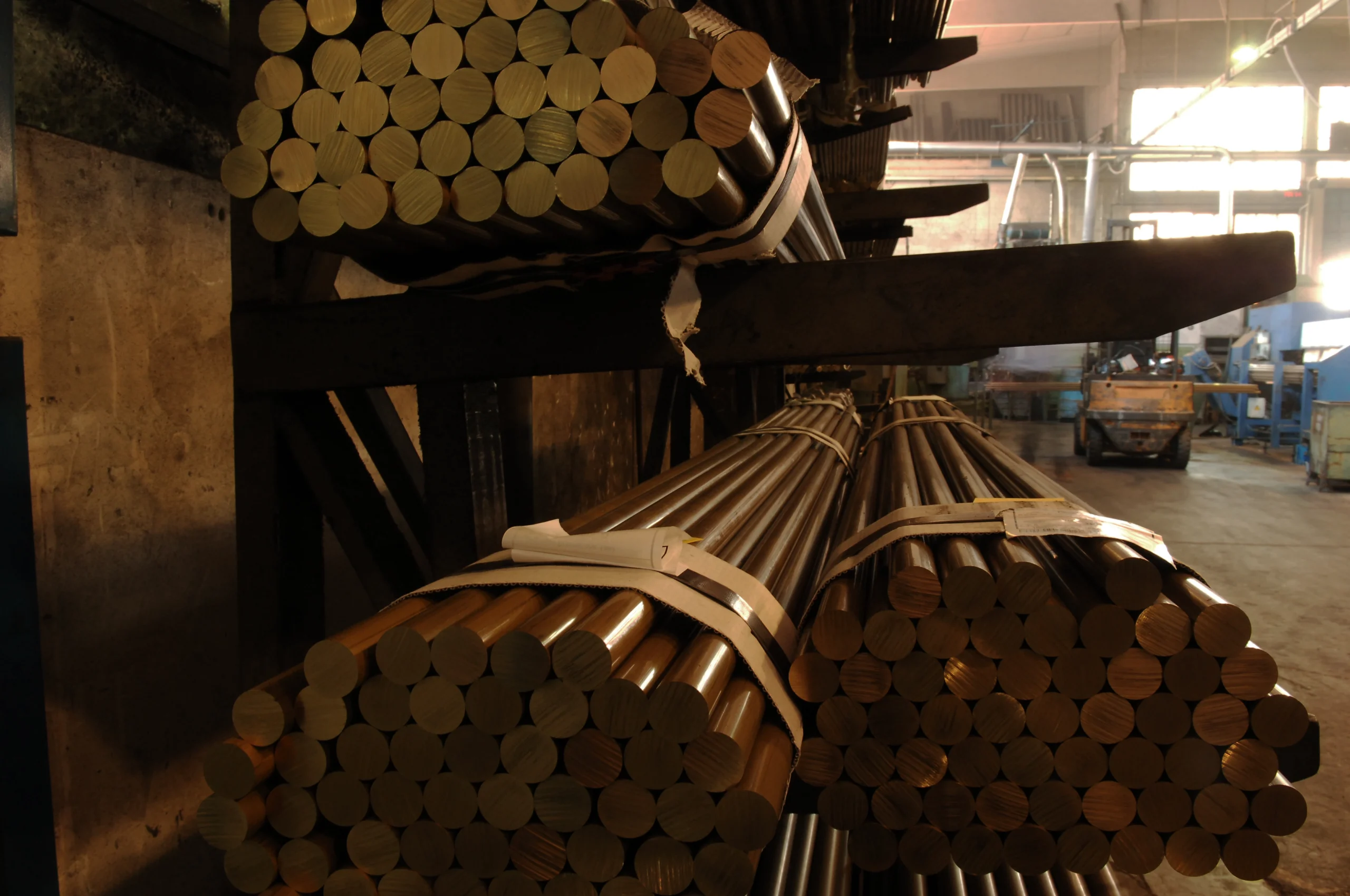
01
Experience
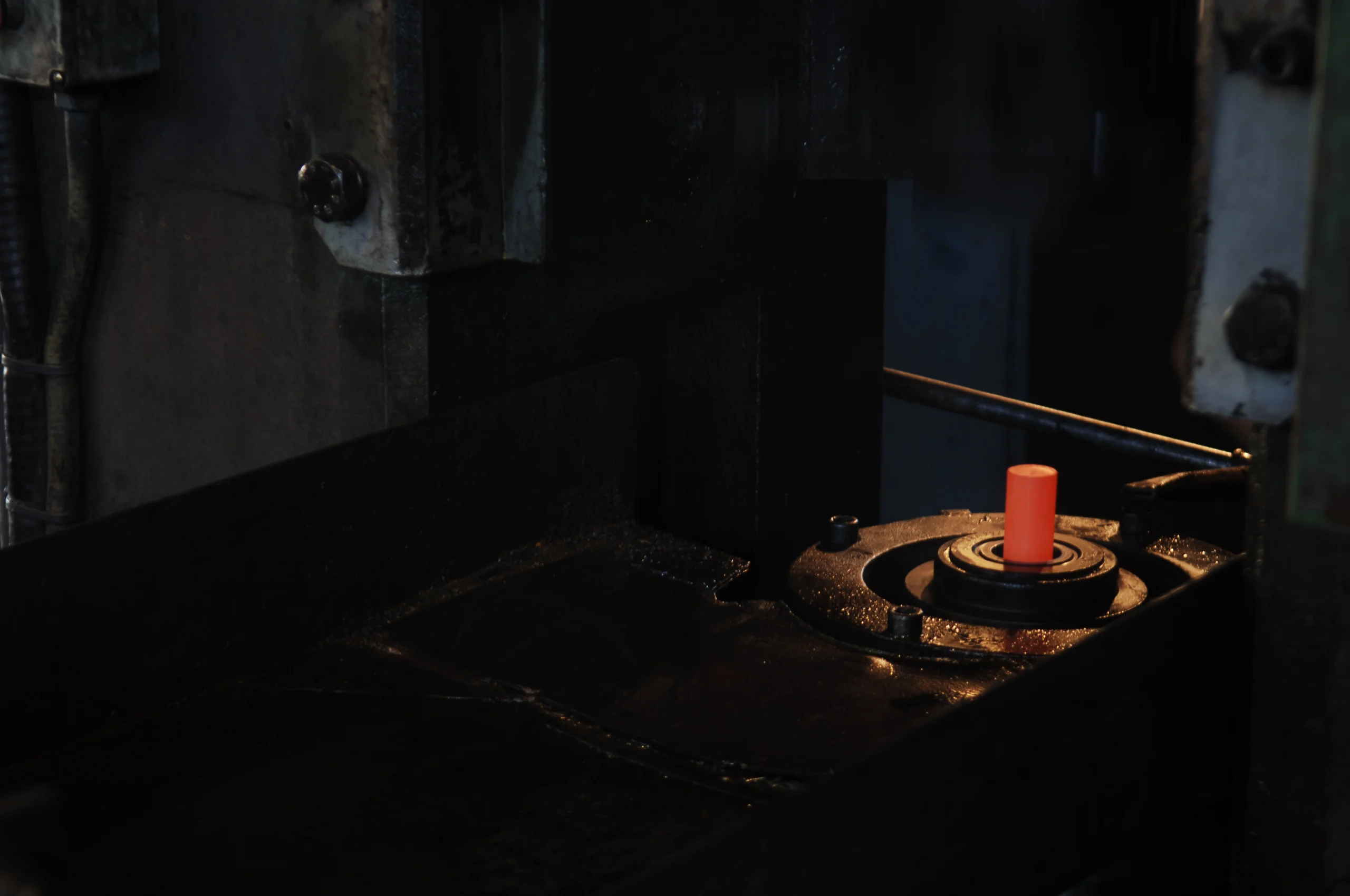
02
Reliability
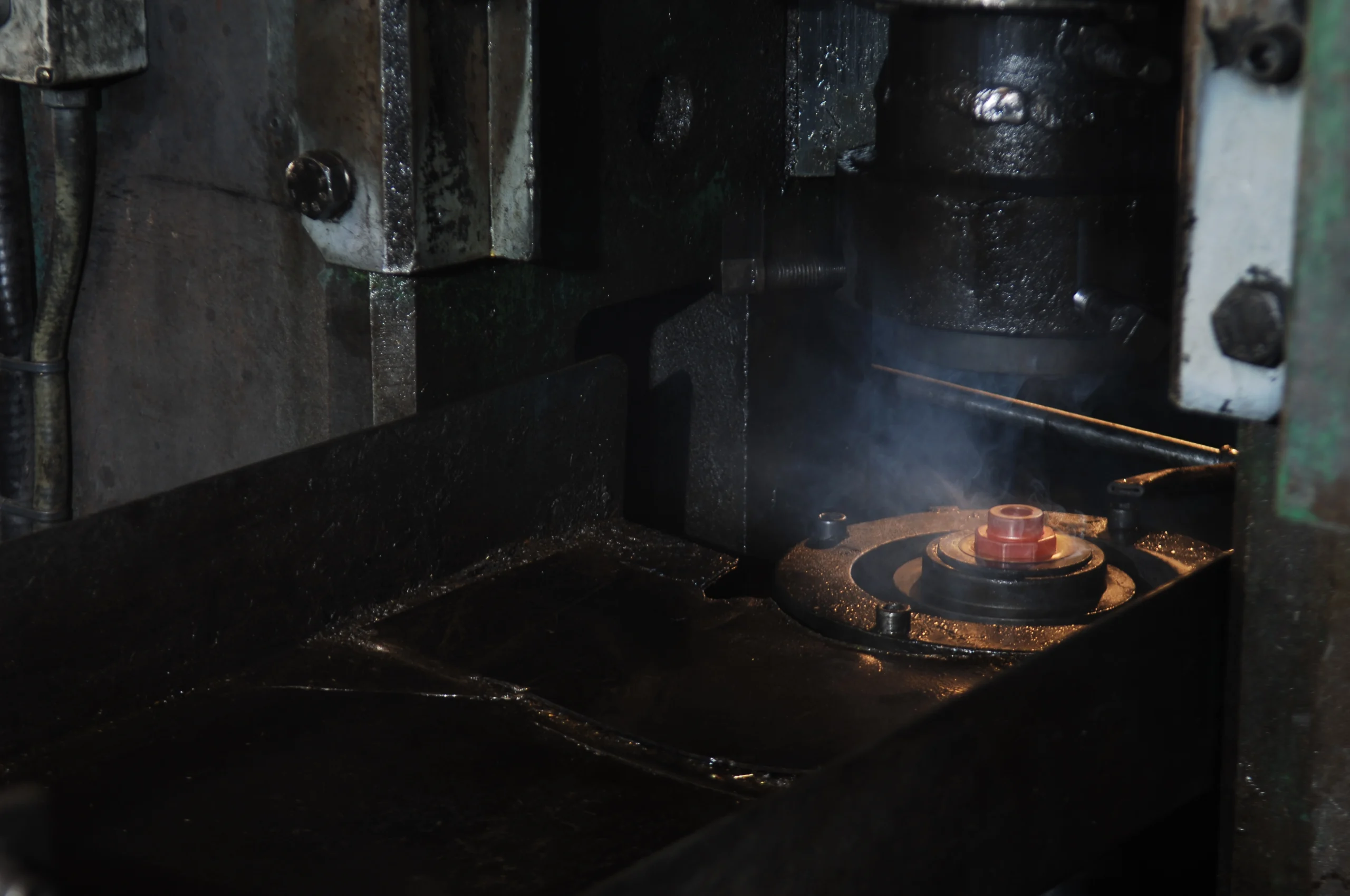
03
Innovation
Fra-Ri Press stands out for its commitment to total quality: all processing phases are carried out internally to guarantee maximum control and optimize quality and timing.
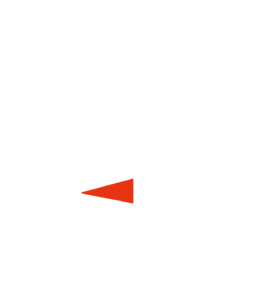
Automatically loaded furnaces
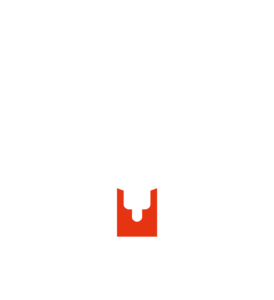
Hot forging presses
BRASS
Brass stamping offers superior dimensional accuracy, tighter tolerances, smooth surfaces, reduced thickness
and increased productivity.
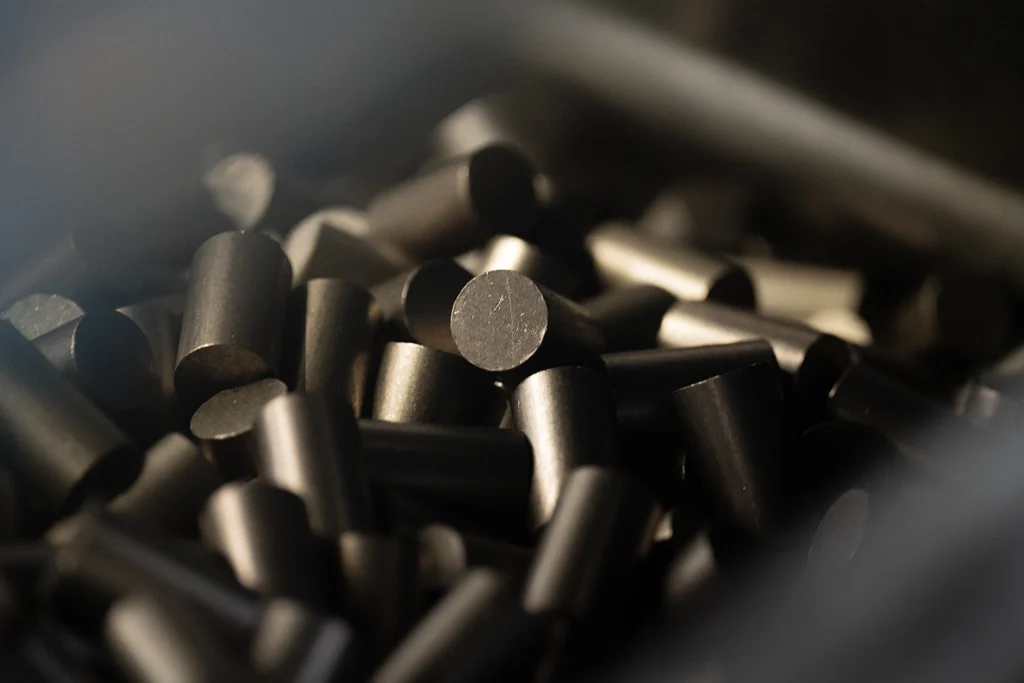
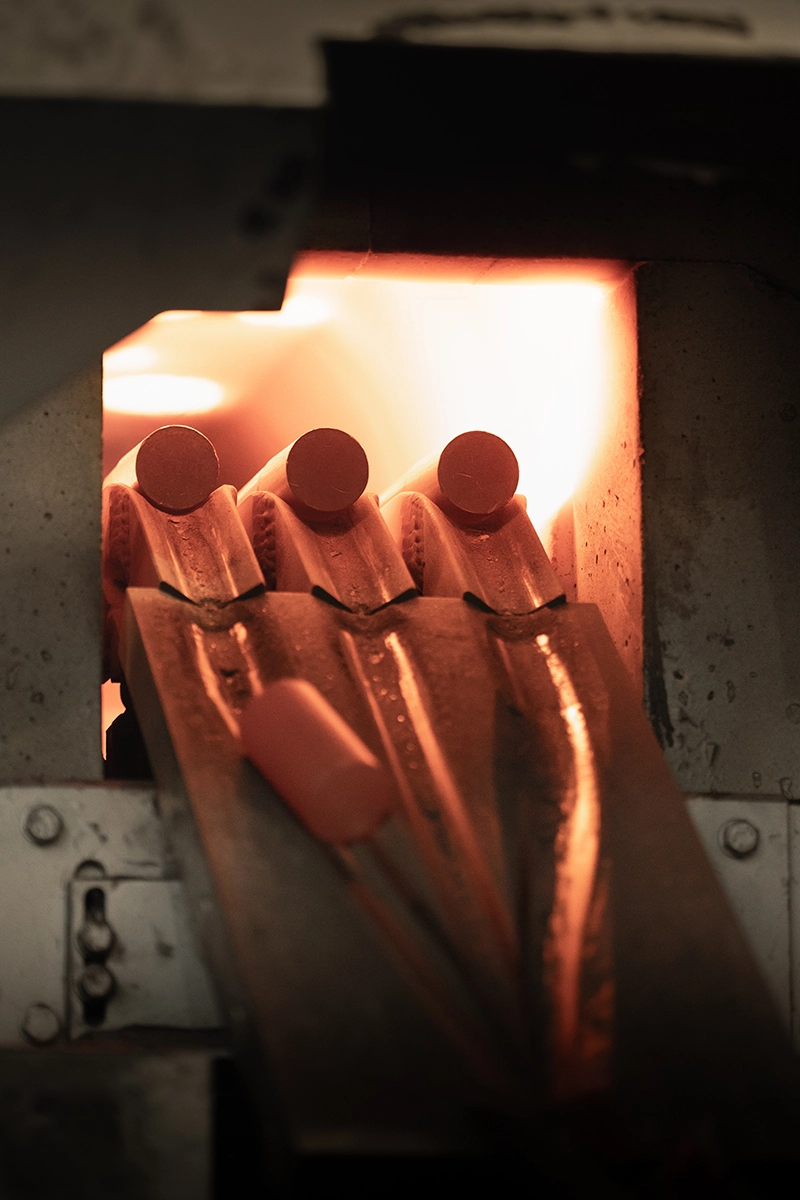
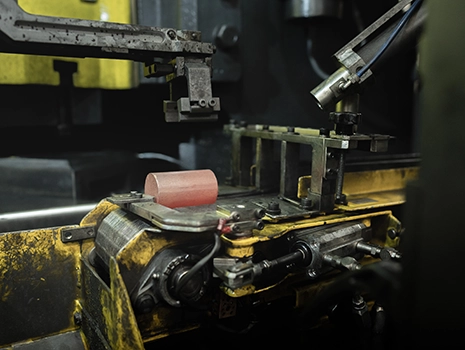
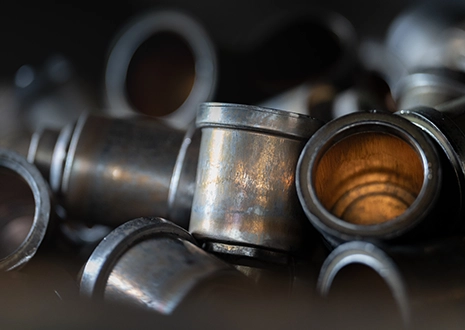
THE PLANT
The modern facilities are divided into specialized departments: raw material warehouse, cutting machines, forging, blanking, and a mechanical workshop for die production and maintenance.
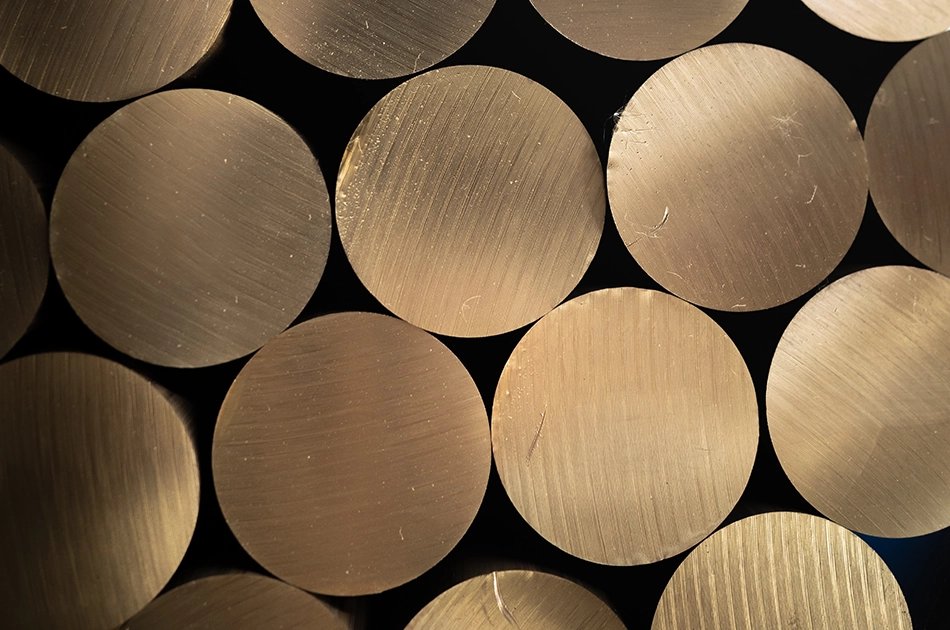
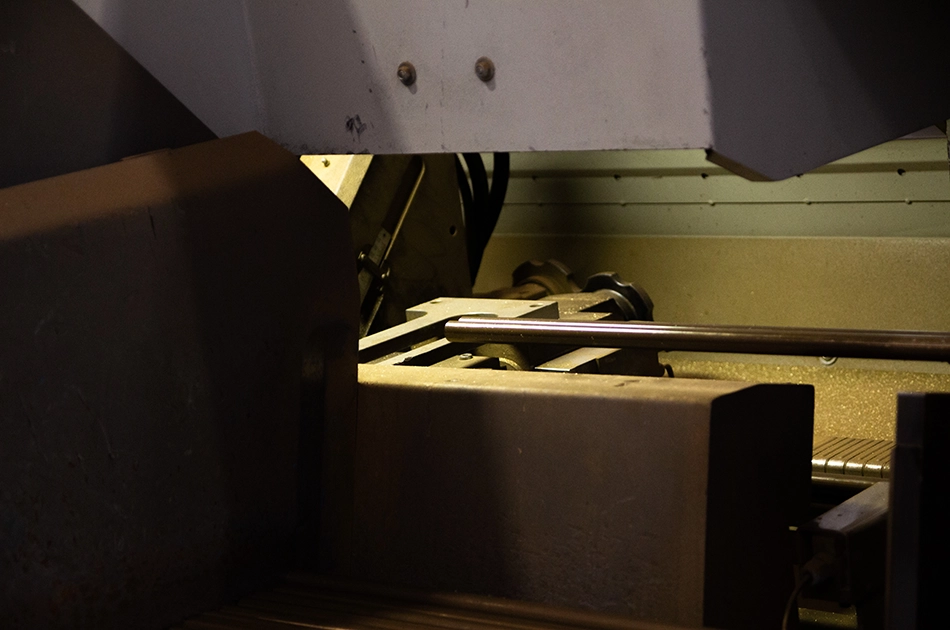
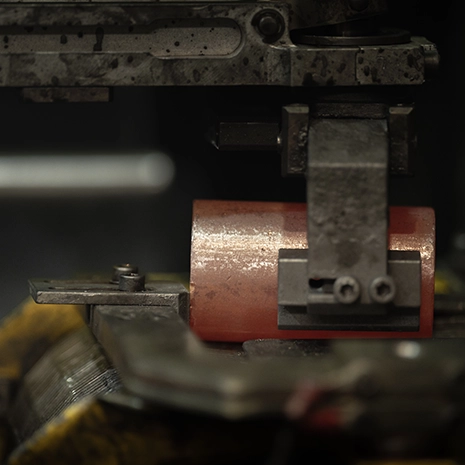
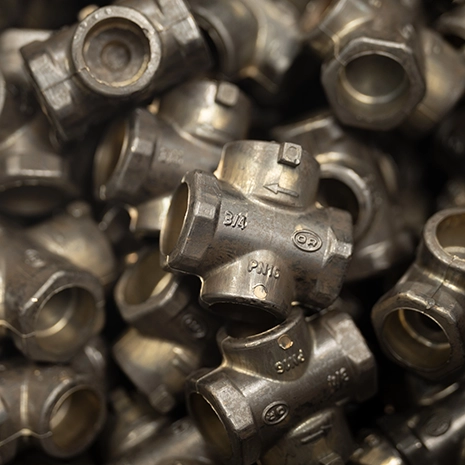
MACHINERY
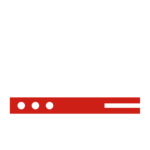
Machines for the automatic cutting of brass bars, producing billets for subsequent forging.
- Possibility of single and double bar cutting;
- Production of up to 65,000 pieces per day;
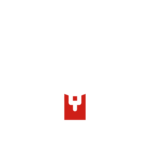
PRESSES
Machines for hot forging brass components. Automatic loading of billets and unloading with a tilting paddle.
- Furnace temperature: 850°C;
- Production: up to 40 pieces per minute;
The department has presses of 200, 270, 400, 500, and 650 tons, and a manually loaded counterblow hammer of 630 tons.
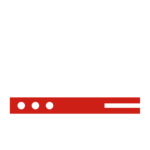
3 deburring presses, internally called “Trance” for finishing parts by removing sharp edges, burrs, fins or material inconsistencies. Deburring improves the surface quality of a part, making it flush for adhesion or joined with other parts, safer, more functional, and aesthetically appealing.
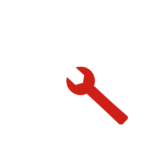
Initially dedicated exclusively to the maintenance of molds and equipment, the New Mechanical Workshop has been transformed into an internal production department for molds and deburring equipment. New equipment has been added, including a Machining Center, two wire EDM machines, a laser engraver for marking stamped parts, a drilling machine, and a Vertical Warehouse (Modula).
CONTACTS
For information, technical and commercial assistance contact us here!